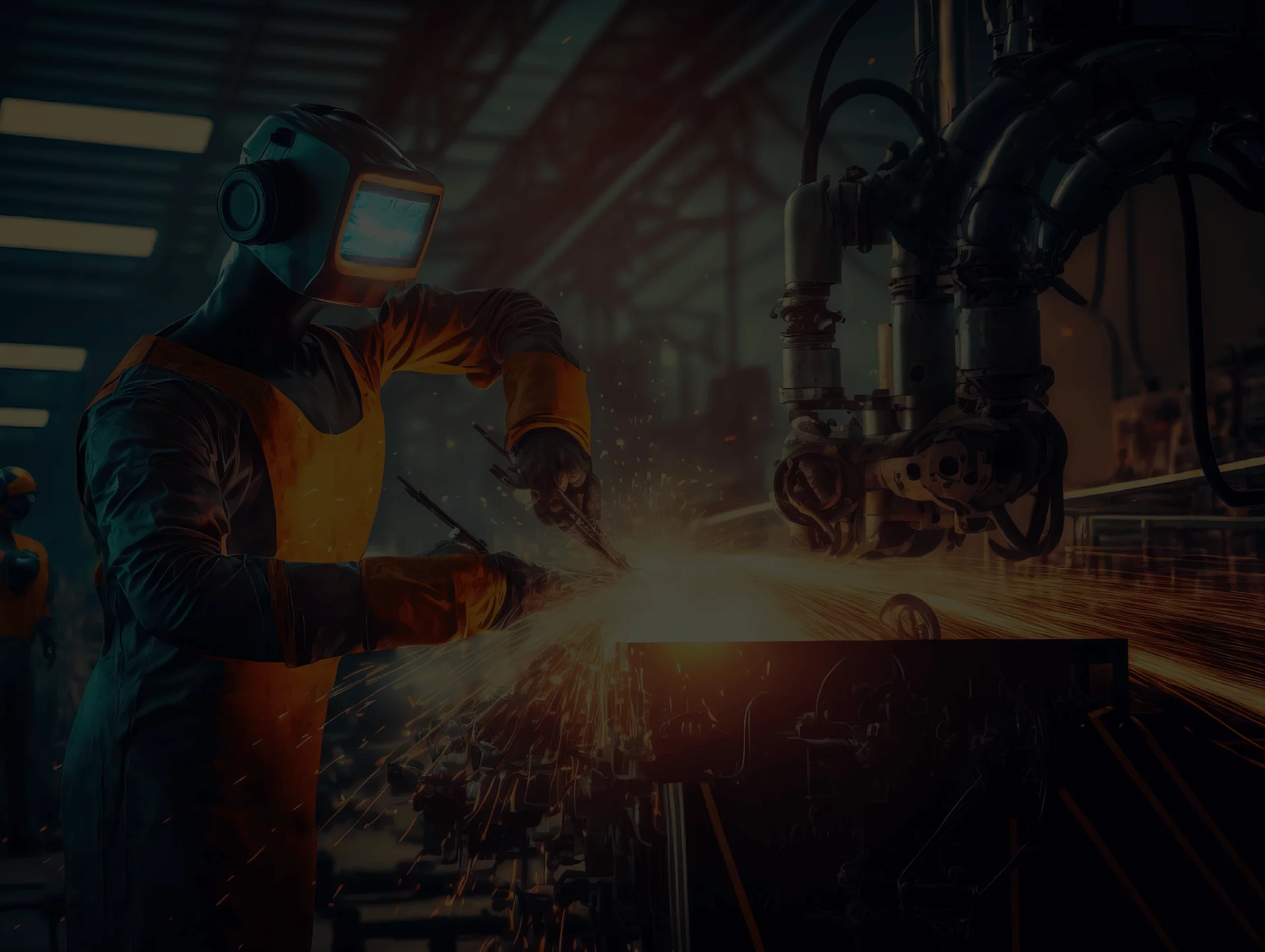
In high-performance vehicles, strength in the cranking shaft area can be improved by installing steel main bearing caps. These will be provided in a semi-finished state and may require some line boring to ensure perfect final alignment before installation.m
Operate your machinery often, and keep it running for long periods. We offer optical device alignment tools that help you check and regulate your machine geometry for straightness, flatness, level, inclination and plumpness, correspondence, and right-angle check.
We have 10 years + of experience providing optical alignment services. We can live for the most difficult alignment jobs, as long as they’re not too hard. If they’re too hard, we’ll probably get bored.
A new optical measurement system has been designed for the simultaneous detection of various geometric errors of machine tools. The system is designed using laser alignment techniques where laser beam measurements are used as the reference datum. The system can measure five error components simultaneously for each moving axis of an industrial robot or CMM.
They are three straightness error components, roll, pitch, and yaw errors. Through actual calibration and measurement, the accuracy of the present system is estimated to be about 2 microns for straightness measurements and less than 0.05 arc seconds for angular error measurements
Flatness is a state of being in which all elements are located in one place. Flatness tolerance specifies a tolerance zone in which the specified surface must lie and is defined by two parallel planes. Flatness is applied by a tool to an individual surface; the flatness tolerance does not require any relationship to a datum. A feature control frame has a leader or extension line attached to it.
When a feature control block with a flatness tolerance value is applied with a size parameter, the flatness tolerance value applies to the median plane of a non-cylindric surface. The derived median plane consists of the midpoint of each local size. The median plane isn’t necessarily flat.
The flatness tolerance controls the shape of the derived median plane, which is used for smoothing out the surface of the mesh. You can use the straightness tolerance to control the form of your derived line.
Flatness controls the waviness or variations in the surface without putting tight constraints on the surface. We use flatness when we need good mating between two surfaces, but the orientation isn’t so critical. Sometimes, designers use a flatness callout to indicate that the entire surface has been worn equally.
First, the laser is roughly aligned along and crosswise with the measurement object. The detector is then placed on the selected measuring points, and the values are registered.
The measurement of flatnesses/twists on circular surfaces such as flanges is based on the use of 3 reference points, situated at 120° intervals around the circle. Determine the number of measurement points for the laser plane and which will be the base points on which the laser will rest.
All measurements displayed are now relative to our laser alignment system which has measurement systems specially designed to check the flatness of flange surfaces for wind turbine towers. The software included assists you with advanced best-fits calculations.
The laser beam is automatically adjusted according to the vial on the laser transmitter, so the measurement value at the initial measurement point is set to 0. The measurement values at other measurement points will show deviations from the horizontal plane.
When referring to cylinder heads, the term line boring refers to the main bearing housings but it can equally refer to camshaft housings where the camshaft is located inside the cylinder head. The line boring operation restores both the size and alignment of these housings so that the rotating components (cams or cranks) turn freely.
With cylinder blocks, one of the most common reasons for needing a line bore is after a crankshaft has failed. A badly worn cranking shaft can “whip” within the main bearing housing distorting them. A seized crankset (due to lack of lubrication or pressure) can result in the chainrings locking into place on the crankset resulting in them being forcibly turned by the chainring teeth which causes distortion and wear.
Similarly, if a seizure occurs inside the camshaft housing where the cam bushes are located, they could be damaged or even rotate within the block itself, causing serious damage. This could result in damage to the housing which would require the housers to be bored oversized, removing the damage and realigning them. Corresponding oversized bushes will be needed to completely repair the damage.
In high-performance vehicles, strength in the cranking shaft area can be improved by installing steel main bearing caps. These will be provided in a semi-finished state and may require some line boring to ensure perfect final alignment before installation.
All or any of the above could mean that your casting needs to be line bored.
Alignment of the drive shaft and the main machine is carried out using a shaft alignment device, which is usually mounted on either side of a coupling. Measurement devices are usually mounted using chain brackets around their shafts or couplings or using strong magnets. Sometimes, one of the measurement instruments can instead be placed on a flywheel of the motor.
We offer laser systems that can measure with as little rotation of the shaft as 40°. Useful if the shaft has difficulty rotating, or if pipe connections and other hull components are in its way. The results of the measurements show how to adjust the motor/gearbox laterally to get the driveline straight. Adjustments to the correct position are made by Live values.
A laser beam can also be used for stern tubes, when the shaft is taken out, along the centerline of the boat. This is what we refer to as boring alignment. An example of a measuring system used for this is because the measurement is performed at the center of the bearing. It is, therefore, suitable for shafts of either small or large diameter.
The measurement method is used to measure the axial displacement of the bearing by mounting a laser transmitter on the axial surface of the bearing journal and placing a receiver in the bearing journal. The measurement value is recorded at a distance from the bearing sleeve as shown on the drawing. The measurement program calculates the position in the vertical axis and the horizontal axis, as well as the first slope and the second slope if necessary. If adjustments need to be made on land or in the water, then compensation values can be entered into the system to correspond with the position in which the vessel is in the sea.
If necessary, the smoothness of the bearing can be checked too. You can use a measuring tape to measure the distance between two points.
Our laser system can measure bearing play: mount a measuring unit on the shaft, and another on a fixed part of the equipment. Raise your shaft (with an aid), and then read off any play.
On water jet drive units, it may be desirable for the unit to be aligned to a mounting flange. A laser transmitter with a built-in angular prism is then needed.
Conventional methods of measuring wind turbines are very time-intensive. With a laser measurement device, work can be done much faster and with greater precision. The possibility of measuring results being easily and recorded is also a great advantage
Electricity production occurs in various forms, including those that rely on turbines for their operation. For example, gas, steam, water (electricity), solar, and wind power. Diesel-powered generators are sometimes used, mainly as a backup and for equalization in power networks. To solve your particular needs for solutions in this application domain, a combination of parts drawn from different measurement systems may prove useful. We have decided to put information about wind power on a separate page, read more about this here.
Older methods for measuring the alignment of turbine blades include using heavy dummy shafts and wire gauges. It takes a long time to set up for measurements. Laser systems come in relatively small and light-weight carrying cases and are set up on the machinery in a shorter time than older methods. For example, there is no wire in between the technician and the equipment, all calculations are done by the software, and alignment can be made with real-time values when appropriate. And of course, there’s a complete documentation of the alignments.
Aligning a diapragm in a gas turbine can be a major challenge. We have a special system for this with flexible and user-friendly brackets and software that guides you through the measurement process. The laser transmitter is usually mounted at one end of a turbine’s centerline (usually a bearing journal) and the detector registers the measurement values from the desired positions. The measurement results display the straightness of the bearings and the diaphragms’ centers, both vertically and horizontally. They compare these measurements against two reference points.
The shaft alignment system ensures that the coupling between the turbine and the generator is aligned properly. Precision is high, so measurement systems can take a large number of measurements at once (multipoint) are required.
The turbine halves’ partitions may need to be checked for flatness. This is accomplished by using a sweep laser transmitter like D22.
It is very important to ensure that the base for the turbine installation is flat and level so that other parts of the installation can be done reliably. Long-term, it is also a requirement for trouble-free operation Our system can help you make sure that is the situation. Other things that can easily be measured and aligned using laser instruments include centering of mount points for sluice gates, straightness of pipe system, squareness and flatness of pipe flanges, and so on.
Checking squareness is carried out by a large number of applications including machine tools, coordinate measuring machines, and mechanical constructors.
To measure squareness first, take two measurements on one object. Record these measurements as a reference for the angle of the object. Next, use the built-in prisms in laser transmitter D22 to deflect the laser beam 90°. Record two new measurement values on the second object. The measurements are converted into an angular measure, showing any deviation from 0° in the second object
Most machine tools rely on the perpendicularity or squareness between moving tables or slides, and also the axis of their travel for a cutting bit or drill. Traditional methods for checking the squareness of machine tools involve using granite squares or jigs coupled with precision dial indicators. The length of time and effort required to perform these alignment checks have been a deterrent to their usage. The development of the Laser Alignment System (LAS) has made the task of aligning squareness much easier, quicker, and considerably more precise than before.
Here’s how it works. A laser reference beam projects down the length of one direction on a machine tool. A digital receiver measures how far the laser beam is from the machine table and uses the readings to guide the position of the laser beam until the readings are equal to each other on the table. The laser reference beam has been aligned with the slide table. At this point, a right angle optic is placed into the laser beam.
All lathes, milling machines, and other machine tools have moving slides or tables which experience wear. Power failures and programming errors can result in machine tool failure and excessive damage to slides or ways when parts of the machine collide. Checking your machine tool for excessive wear and damage can be done easily and straightforwardly using a laser alignment system.
These checks allow you to
Assess the standard levels of wear and tear.
Determine if damage to the machine has occurred.
Provide information for repair.
Maintain ongoing preventative maintenance activities to ensure that everything continues.
Using a laser alignment system can be an effective way to align
Setting up the laser system on a machine tool isn’t difficult. In the following example, we will show how a Laser system is set up and measure the position of an X-axis slide table using a laser. The laser transmitter is attached to a tripod to the side and adjusted so that the reference beam over the top of the slide is measured. A quick bucking in the process helps align the lasers so it is parallel with the travel of the table.
Next, we mount our digital receiver on the table using a magnetically attached mount. We connect our digital receiver to a display unit that displays the position of the receiver from left to right, as well as up and down. The display on the Laser Alignment System provides a precise readout to within 0.0001 inches (0.25 microns).
As the slide table continuously moves the receiver, it checks its position, relative to a laser reference beam. Any movement left or right or up or down is quickly seen and noted.
A quick alignment evaluation can be done by simply watching the laser aligner display and slowly moving the stage or slide along with its movement and noting any variations in reading. The laser alignment system may also be connected to a computer for collecting and storing readings.
In many places, you need to ensure that the surfaces are perfectly straight, e. g., when using a lathe, CNC, etc.
It is desirable that the tool moves during a straight path to obtain the perfect cylinder and it is possible only when the guiding guideways are themselves straight Line or plane is the basic unit of measurement for most methods of measurement. The standard of straightness in precise engineering is represented by a ruler. According to Bryan’s Principle, a straightness measuring device should be aligned with the functional point at where straightness is to be determined. If this is often difficult, either the slideways that transfer the measurement must not move at an angle or angular motion data should be used to calculate the result of the offset.
A line is considered straight if the variation of the distance between any two points on the line from two planes perpendicular to the line and parallel to the line itself remains within the required tolerance limit. The reference planes are so chosen that their intersection lies parallel to the line joining two points on the road to be measured.
Therefore, the two points are close to the ends of the lengths to be measured. The straightness tolerance is defined because the maximum allowable deviation from the reference line joining the two ends of the road is to be inspected.
It is the standard procedure to state the range of measurements, i.e., to check the length; and the position of tolerance about the reference line. output must be a single paragraph. Most often, the parts at the very edge of the ends, which usually have local errors of no major importance, may be neglected or ignored.
Straightness is measured every day in several industries. as an example, for instance, members, rollers; pipes, the machine ends; machine runners, and conveyor belts. Straightness measurements are taken for bearing positions, for example, in diesel engines. Straightness is usually an important requirement for a machine to operate correctly and/or produce fault-free components.
The basic principle of Straightness Activity is that each activity value shows the position of the detector relative to the sunlight beam. the sunlight beam could also be visualized as a very, very, long, fully straight, weightless ruler. First, the beam must be roughly aligned with the activity.
It is the standard procedure to state the range of measurements, i.e., to check the length; and the position of tolerance about the reference line. output must be a single paragraph. Most often, the parts at the very edge of the ends, which usually have local errors of no major importance, may be neglected or ignored.
Straightness is measured every day in several industries. as an example, for instance, members, rollers; pipes, the machine ends; machine runners, and conveyor belts. Straightness measurements are taken for bearing positions, for example, in diesel engines. Straightness is usually an important requirement for a machine to operate correctly and/or produce fault-free components.
The basic principle of Straightness Activity is that each activity value shows the position of the detector relative to the sunlight beam. the sunlight beam could also be visualized as a very, very, long, fully straight, weightless ruler. First, the beam must be roughly aligned with the activity.
With our laser alignment tool, you’ll be able to check the straightness of any round profile inline and with just one measuring routine. The measuring frame is designed to be installed directly into your existing line and contains at least three pairs of measuring sensors the thing rolls through a measurement system within an inspection process and is scanned The measurement result shows how far off the straightness of a line is from the straightness of a reference line. You may optionally set additional parameters like the length (or diameter) and ovality of the object.
Parallelism could also mean whether two things are parallel or whether two lines are perpendicular to each other. Parallel simply means that there are no gaps between the surfaces or the two lines. If the surfaces or shapes were extended on paper to infinity they would never meet.
In device alignment, the red beam is the reference for measuring the correspondence. Compared to recent technology (such as smartphones), the work is done faster, easier, and much more accurately. the sunbeam has no weight or volume It’s compact, versatile, and easy to use when the need arises. The versatile style allows production teams to unravel the manufacturing issues on-site quickly. this might cause unnecessary machine breakdowns and expensive repairs. It’s additionally attainable to identify placement within the time frame, before there’s a breakdown, and carry out preventative maintenance work.
You can also make a profit by documenting the alignment job. Another advantage is that devices can also be used for various other alignment activities, such as flatness activity of wire segments (suction boxes) or shaft alignment of drive units It makes it a very cost-effective investment for the maintenance department. Correspondence activities include correspondence between rolls and different materials in printing presses, rolling mills, and so forth. different examples include overhead tracks, rails, and press machines.
When you’re rolling strips of material through a web process, rolls that are out-of-parallel alignment can have a big effect on the direction of strip movement, quality of product, tension, wind-up, printing issues, wrinkles in the product, and tear-outs if the misalignment isn’t corrected.
These problems cost the company money. Slowing down a process to assist in controlling steering decreases the quantity of the product being manufactured. Adding unnecessary and expensive bowed rolls to assist relieve wrinkles, and installing steering rolls to help guide the online, adds complexity and more interaction between rolls, which costs money and effort. In such cases, production is halted once the merchandise tears out or if the wind-up is too poor for the finished product to be used.
A potential explanation for almost every web defect is the misalignment of the method rolls. It doesn’t mean that it’s always the cause. Just a possible cause. Eliminating roll parallel alignment allows for easier troubleshooting if problems are not resolved after the alignment of the roll has been completed.
Almost all of the analog measurement techniques are “subjective,” instead of “objectively” measured. Plumb-bob, optical transits, and dial indicators are completely hooked into the user. Tram-rods and pi-tapes, however, are not. Everybody will see something different when they’re rummaging through a bus or train. Dial indicators have sags within the fixtures and any views of the dial from edges aside from straight on lead to a parallax issue. Feeler gauges are only accurate because of the person who slides them behind the perpendicular. They are subjective.
The laser beam emitted by the transmitter is the most accurate reference we will have. When that laser hits the sensor, the position of the object is shown on the display unit. Inputs If the amount is $10.20, I see $10.20, that $10.20 value won’t change if someone else watches it. that’s an “objective measure
Another reason why I prefer laser technology over ultrasound technology is the speed of finding out and therefore the compactness of the equipment. Optical tooling is large, heavy, and labor-intensive to align properly and accurately. By comparison, the lasers are lighter and smaller and are far more portable than the traditional equipment. Time and Measurement Time Are Wasted Time If facilities aren’t making products they’re losing money. If half the alignment time is spent fixing equipment, then the alignment isn’t getting done. Some facilities lose up to $50,000 per hour. Quickly getting the alignment data and getting the alignments right makes my customers very happy.
The documentation of the results is crucial. As the rolls are measured, moved, and verified, the results of the measurements are stored within the display. At the end of the day, the report is transferred to a USB stick, and therefore the report is provided to my client.
The purpose of leveling, also known as leveling, is to establish, verify, or measure the height of specified points in relation to a datum. It’s commonly used in geodesy and mapping to determine the geodetic height, as well as in construction to determine height disparities between building artifacts. It’s also known as differential leveling or spirit leveling.
After the operator has roughly leveled the instrument, an automatic level uses a compensator to keep the line of sight horizontal (to within maybe 0.05 degree). The surveyor can swiftly set up the instrument and does not have to relevel it each time he sights on a rod at a different place. In addition, rather than leveraging the tilt over the sight distance, it reduces the effect of minor tripod settling to the actual amount of motion. The instrument is leveled using three-level screws.
When using an optical level, the endpoint may be beyond the instrument’s effective range. Between the ends, there may be obstacles or significant elevation variations. Extra settings are required in these circumstances. Moving the level to take an elevation shot from a different point is referred to as turning.
To “turn” the level, take a reading and write down the elevation of the spot where the rod is. The level is shifted to a new point where the rod is still visible while the rod is kept in the same place. A reading is taken from the level’s new location, and the height difference is used to determine the level gun’s new elevation. This process is continued until all of the measurements have been taken.
To get a proper measurement, the level must be horizontal. As a result, if the instrument’s horizontal crosshair is lower than the base of the rod, the surveyor will be unable to sight the rod and obtain a reading. The level may normally be adjusted much higher than the rod’s base because the rod can be elevated up to 25 feet high.
The alignment of your production machinery is critical for maintaining optimum equipment performance and producing the highest quality products.
The plastic extrusion process is no different. With increasing demands for extruders for faster speed and better quality, it’s more important than ever to ensure proper maintenance of the equipment that makes up this process.
A typical single screw machine has four main parts: a gearbox, a feed throat, a barrel, and a feed crew. Maintaining the correct alignment of the rotational axis of the screw to the axis of rotation of the gearbox thrust bearing is one of the most important factors in ensuring maximum efficiency. If these components are misaligned, excessive contact may result which could lead to:
Early barrel and screw wear
Increased clearance
Reduced throughput
Back-flighting
Poor mixing
Uneven melt temperatures
Surging
Screw flex
Screw breakage
Misalignment can often be caused by many different factors, including maintenance procedures, barrel/gearbox/motor installations, and machinery conversions and upgrades. Fortunately, there are ways to align your body and mind that can significantly help to reduce misalignment-related issues.
Two primary methods have traditionally been used for measuring extruder alignment—optical alignment tools and laser-based alignment systems.
Precision optical equipment, such as telescope transits or dual-axis sights, is used to measure angles. An optical instrument is a tool used to align the extrusion barrel to the gearbox. On the eyepiece of an optical instrument, there is usually a reticle (or a crosshair). It is set to infinity. An optical alignment engineer establishes a line-of-sight reference using an instrument. With the use of an optical target along the barrel, the gunsmith can measure any radial displacement of a centerline of the barrel from its line-of-sight position.
Like the optical alignment method, a laser alignment system is placed on the gearbox shaft and then adjusted so that it is aligned with the centerline of its thrust shaft. Laser alignment systems use a laser beam and light-sensitive targets that are moved along their length. When the target detects the laser beam, the measurement data is displayed on the digital display.
Both optical alignment and laser alignment systems are highly precise and will perform well to measure the misalignment of the gearbox and barrel.
It is recommended that wear testing of both the barrel and screw be performed regularly to accurately predict when new equipment may be required. If you perform troubleshooting measures early after you notice the first symptoms, you can help to ensure that issues are addressed before they can cause extensive damage to the components, thereby extending the life of the equipment for longer. Preventative and troubleshooting measures include:
Vtech Maintenance & Services specializes in Alignment Solutions with advanced laser technology.
© Copyright 2024 All rights reserved.